We began our continuous improvement journey at BSA LifeStructures in earnest about nine months ago. In that time, we’ve established pockets of teams and departments that have embraced the continuous improvement culture. These people have proven to our leadership that continuous improvement should be a permanent part of BSA LifeStructures. We’re using KaiNexus to help us quantify the impact of improving our methodology and our culture.
When we started out on our continuous improvement journey, we knew that we had a lot to learn. Looking back now on what we’ve accomplished and how we as an organization have grown, it’s hard to imagine that we’re only nine months into it. If I knew then what I know now, we’d have done some things differently. It’s not so much that we made mistakes, you see, but rather that we’ve since identified opportunities for improvement in our improvement process. I’ll share them with you here in the hope that someone is able to learn from our experience.
My first piece of advice to my nine-months-ago self would be to never underestimate the importance of a simple, consistent, and disciplined improvement methodology. Without this structure, the idea of building a culture of continuous improvement and spreading new ideas as standard work is very difficult.
A lack of consistency across the organization results in two critical problems:
-
It’s harder to get people to participate in the improvement culture if it’s not something the entire organization is engaged in. This makes the role of middle managers in driving adoption much more difficult. Having a regular forum to talk about continuous improvement increases engagement by reinforcing the idea that this culture is to be the “new normal” for the company.
-
An inconsistent methodology makes it nearly impossible to create standard work. Because new ideas don’t get spread across the firm if continuous improvement only exists in little pockets, improvement in each pocket really just creates more process variability. By implementing a consistent improvement methodology, ideas can spread and processes can improve firm-wide.
I recognize that methodology isn’t something that can be changed instantaneously. Our firm is spread across seven offices with ten different client delivery teams, in addition to corporate and construction administrative services. In order to enact change and an improvement methodology, we have to touch all of those offices. Even with the organizational structure in place to execute the methodology, many places and teams in the firm may not execute the methodology as it exists on paper. When we first started our improvement journey, I knew that solving these problems wouldn’t be easy; nine months later, I stand by that assessment.
So how do you do it? How do you implement a consistent, disciplined methodology in an organization that is so complex? The answer is leadership.
The managers and leaders of different departments in our organization view continuous improvement differently. This results in a discrepancy in the amount of focus placed on standardizing work – with some managers not addressing it at all. We knew right off that bat that we needed to get senior leadership buy in for continuous improvement, and that definitely helped.
My advice to you, though, is to focus on getting middle managers on board too. These are the folks that encourage the staff to identify and implement opportunities for improvement. Their exchanges with staff are often the first communication about submitting ideas, solving problems, and coaching others. They really are the front line leaders responsible for driving culture change across the organization. If I knew then what I know now, I would have done more research to see what each of these folks are doing with their team in real life, in an effort to understand the current state of their methodology. After all – you should always seek to understand the current state before diving into improving it, shouldn’t you?
My advice is to then coach the middle managers on how to be better leaders of continuous improvement. I recommend spending time understanding who will be champions for continuous improvement, and perhaps engaging a few more people to fill that role. Coaching them in the behaviors that engage people in improvement is key to their success. Teaching them how to ask the right questions and engage the right people will ultimately improve the results of their teams’ work, as that knowledge will trickle down to the front line workers.
So what are we doing now that we’ve learned these lessons?We’re continuing to improve our methodology across the firm, to make it even more consistent and disciplined. We’re also striving to engage more of our employees in the culture change, and to recruit people who are energized by continuous improvement. At BSA LifeStructures, we’re working to empower ALL of our people to solve what bugs them, what needs fixing, and to improve processes that don’t contribute to the success of our clients.
What have you learned in your continuous improvement journey? What advice do you have for organizations that are setting out to change their culture?
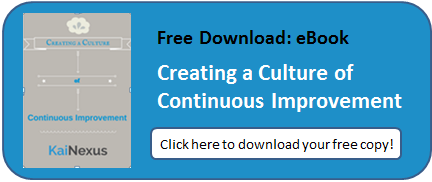
About the Author:
Jake Snyder is a design engineer at BSA LifeStructures, and is one of the firm’s staunchest advocates for Lean implementation on design projects. Jake has also been an office leader in the firm’s own adoption of Lean principles. A Lean Healthcare Yellow Belt and Six Sigma Green Belt, Jake has already created measurable improvement using Lean methods at one of the nation’s premiere healthcare projects, the Simon Family Tower project at Riley Hospital for Children at IU Health. Jake is recognized for his work within complex environments that require creative, high-performance engineering solutions.
Add a Comment