What is Process Improvement?
Process improvement is a method to eliminate friction in processes that leads to project delays, employee disengagement, and productivity decline. It starts with a clear understanding of business goals and involves a continuous cycle of incremental change. Organizations have used business process improvement, sometimes in the context of total quality management, to reduce waste, increase operational excellence, improve customer satisfaction, and better utilize existing resources.
How Does Process Improvement Help Businesses?
Process improvement helps organizations meet market demands and accomplish business goals with little waste. Process improvement relies on the idea of comparison; what gets measured improves. It is used widely to bring order to unreliable processes and align all operations with the enterprise goals.
Implementing process improvement and the related techniques is a project that requires a precise aim to see results. The goals of process improvement include:
- Assess existing processes, their relative efficiency, and their roles in the company
- Identify how misaligned processes could be better synchronized with the organization’s goals
- Define how the improved results would add value to the operation
- Identify and reimagine available resources for an effective process improvement implementation
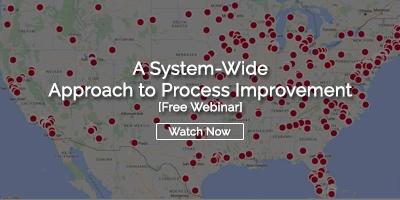
Process Improvement Techniques
Perhaps the best way to describe the meaning of process improvement is to explain some of the tools and techniques used to achieve it. While there is no “right” way to do it, the following techniques are widely used because they have proven effective.
Standard Work
We mentioned earlier that process improvement involves comparing the current state to the desired state. This is difficult if a process is not operated consistently. That’s where Standard work comes in. Standard work is the documented current best practice for any function or task. Every process operator conforms with the Standard until an improvement cycle is completed and a change is implemented. Thus, standard work is the foundation for business process improvement.
The PDSA Improvement Cycle
PDSA stands for Plan, Do, Study, Act. It is a simple yet powerful way to structure improvement. During the first phase (Plan), the current process is analyzed, the project’s goals are identified, and a hypothesis about what change will result in improvement is reached. In the next phase (Do), the agreed-upon modifications are implemented. Next comes Study. Now, the results of the change are measured against past performance to determine if a positive change has occurred. In the final phase (Act), changes that did result in improvement are put into the Standard, and a cadence for future measurement is defined.
A3 Problem-Solving
The A3 problem-solving technique works hand in hand with PDSA. On a single sheet of paper, teams document:
- Background: This is a description of what needs to be fixed and an argument for solving it.
- Current State: This is a data-centric measurement of the current process results.
- Problem: This section includes a root-cause analysis that defines the heart of the issue.
- Future State: This area details the project’s specific goals and any countermeasures to the specific issue.
- Implementation Plan: Now, the Who, What, and When of the intended change is addressed. This section includes timing, the team members, and a plan for assessing results over time.
- Results: Once the change is implemented, the team compares the results to the plan and considers the total long-term effect of the project on the organization.
Rapid Improvement Events
Although process improvement should happen daily, some problems are so severe or opportunities so significant that it makes sense to pull the right people off their regular work to focus on the issue for a three to five-day span. These are called rapid improvement or Kaizen events. A skilled facilitator brings together process operators, subject matter experts, and the “customers” of a process to define the current and ideal states, perform a root cause analysis, consider possible remedies, test proposed improvements, and document the results.
The 5 Whys
We mentioned the importance of solving the root cause of a process problem rather than simply fixing the symptoms. The 5 whys is a helpful technique for doing exactly that. You begin with a problem statement and then ask “Why” as many times as necessary (usually around 5) until you get to the real reason for the issue. For example, if a contact center has an increasing rate of abandoned calls, leaders may ask “Why” several times to find a problem with the employee scheduling software.
Process Improvement Examples
We’re fortunate to be in the position to chat with folks involved in process improvement every day. While every organization is different, here are some simple yet impactful improvements our customers have implemented.
Change Meeting Times
Texas Health Resources realized they were adding to staffing costs by holding staff meetings when staff members weren’t regularly scheduled to work. This resulted in an additional cost of $1,800 a month to pay for the extra hours worked. To eliminate this waste, the team found a way to schedule the meetings during regular work hours.
Skill-Based Routing
A contact center found that their first call resolution rate was decreasing, leading to reduced customer satisfaction and agent fatigue. To solve this problem, they implemented skilled-based routing, allowing customers to use the phone system to select a problem category and be routed directly to an agent with the training needed to solve the problem. This solution allowed them to improve their first call resolution rate by 37%.
Improved Facility Layout
A shirt manufacturing operation was able to operate with acceptable performance when they processed an average of 5,000 shirts a month, but when they grew to 8,500 shirts, errors increased and the operation buckled under the pressure. Analysis showed that employees walked an average of 193 feet during the processing of each shirt. The team also discovered that outbound and inbound shipments were sometimes confused since there was only one loading dock. By rearranging the workstations and using visual management, errors were reduced by 75%.
The meaning of process improvement is somewhat different for every organization, but the bottom line is that there is always room for positive change. The more people you involve in analyzing processes and implementing incremental improvements, the faster you can achieve your business goals and delight customers.
Add a Comment