There are dozens of tools and techniques used by organizations to support their continuous improvement efforts. The most successful companies I've seen pick a few methodologies that work well for them and execute them consistently. If improvement work slows down or a new challenge arises, they experiment with another technique. Whether you are just getting started with structured improvement or if your practice is mature, you might consider adding a tool known as the Kanban methodology. This post will cover the meaning of Kanban and a few of its key advantages.
What Does Kanban Actually Mean?
We tend to think of just-in-time manufacturing as a relatively new concept. Dell builds your PC when you order it, but does it quickly, so you are satisfied with the speed of delivery. Plus, Dell never has excess PC inventory on its hands. However, the idea is not new at all. In the 1940s, Toyota began applying the principle to its production lines after taking a lesson from an unexpected place: the grocery store.
The word kanban means signboard or billboard in Japanese.
When you go to the grocery store, it's rare to find an empty shelf. (Pandemic-related supply chain disruption, notwithstanding.) If you do find items missing, the shelves don’t stay empty for long. The reason is that the store has both the inventory on the shelf and some inventory in its own on-site warehouse.
While shopkeepers know that the store will lose money if they are out of an item that a customer wants to buy, they don’t want to stock more of a commodity than will be sold in a short enough time to ensure that the items are fresh. They also don’t want to tie up capital in inventory that is just sitting around. So, when a shelf is depleted, it is refilled from the on-site inventory, and only then are new items ordered from the manufacturer to replace the warehouse products.
Toyota realized that the same management technique would work for items needed on its manufacturing floor. They further enhanced the idea by adding Kanban cards, which served as a visual signal of the state of inventory. The approach can be applied to any business process with work in progress, so its use is not limited to the manufacturing of hard goods.
How Do the Four Kanban Principles Work?
What Does "Visualize Workflow" Mean in Practice?
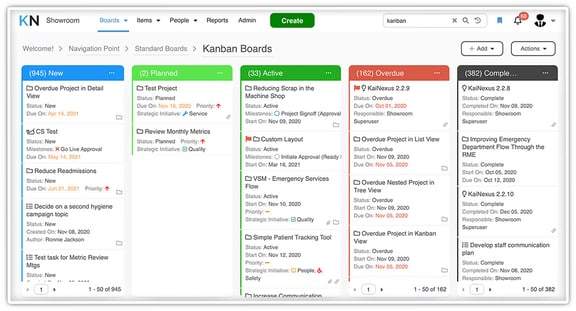
Given the origin of the word, it isn’t surprising that the first principle of Kanban is about visualization. Unlike some business process approaches, Kanban doesn’t prescribe a workflow; it only requires that work in progress be managed in a way that can easily be visualized. To begin a Kanban improvement, it is important to visually map the process as it currently exists.
What I've observed repeatedly from visualizing workflows:
- Teams gain an immediate understanding of work distribution
- Bottlenecks and inefficiencies become obvious within days
- Communication improves dramatically when everyone sees the same picture
Visualization continues once Kanban is implemented and communicates the state of projects, processes, and inventory.
Why Should You Limit Work in Progress?
The goal of Kanban is to move every bit of work efficiently from beginning to end with as little waste and lag as possible. This requires limiting the amount of work in the pipeline to what can reasonably be managed at a given time. This is where I see the most resistance from teams initially, but it's also where I witness the most dramatic improvements. Work-in-progress (WIP) limits prevent system overload:
- Set maximum limits for work items in each column or stage
- Pull new work only when capacity becomes available
- Focus on completing existing tasks before starting new ones
- Establish clear policies for when and how work moves forward
Like in the grocery store, inventory is pulled from the backroom to the shelf only when customer demand makes space for it. The Kanban approach moves work from one stage to the next only when it is pulled through by “customer” demand. Work is never pushed forward, so bottlenecks are avoided.
How Do You Focus on Flow Effectively?
When the first two principles of Kanban are in place, workflows flow freely. Your attention, therefore, should be focused on any interruptions in flow, which represent opportunities for additional visualization and process improvement. Flow optimization involves monitoring and improving how work moves through your system:
- Track cycle times from start to completion
- Identify flow interruptions and blockers immediately
- Measure throughput and delivery predictability
- Address impediments as soon as they're discovered
What Does Continuous Improvement Look Like?
Kanban is something that is never “finished.” The approach requires constant monitoring and analysis to look for the next best way to improve. Conditions, resources, and customer demands change over time, so it is essential to assess flow and look for blockers or friction that teams can remove.
- Conduct regular retrospectives to review what's working and what isn't
- Make data-driven decisions using flow metrics and team insights
- Experiment with process changes in small, measurable increments
- Adapt to changing requirements and market conditions
What Are the Main Benefits of Using Kanban?
With this kanban definition in mind, the benefits of the technique become clear. Including:
- Get Quick Insight – People comprehend visual information much faster than they process text. You only need to look at a Kanban board or card for an instant to understand the current state of work in progress.
- Identify Blockers – It might help to think about work as going in one end of a pipe and coming out the other. It goes in one state and comes out as something with more value. However, if you keep stuffing things into the pipe and nothing comes out, you’ve got a problem. Kanban boards and cards help avoid this problem by making it obvious when and where work is getting stuck and enabling managers to take the steps necessary to solve the problem.
- Predict Results – Managers who have reasonable control over work in progress can quickly and accurately predict when projects will be completed. They know in advance if there is any reason to fear that deadlines will be missed. The Kanban method helps improve predictability by maximizing and visualizing flow.
Frequently Asked Questions About Kanban
What's the difference between Kanban and Scrum?
Kanban is a continuous flow method without fixed time periods, while Scrum uses fixed sprints (usually 2-4 weeks). Kanban focuses on optimizing flow and can be implemented alongside Scrum in a "Scrumban" approach.
Can Kanban work for non-manufacturing industries?
Absolutely. Kanban principles apply to any work that moves through multiple stages - software development, marketing campaigns, healthcare processes, legal workflows, and professional services all benefit from Kanban implementation.
How do you handle urgent work in a Kanban system?
Create clear escalation policies for urgent work, potentially including:
- Express lanes for critical items
- Expedite policies that allow WIP limit exceptions
- Service level agreements for different work types
- Regular review of what constitutes "urgent" work
How often should you review and adjust your Kanban system?
Conduct weekly operational reviews to address immediate flow issues and monthly retrospectives to evaluate and adjust the system itself. Major process changes should be implemented gradually and measured for effectiveness.
Add a Comment