In a recent webinar titled Taking Improvement Boards Digital: How Leading Companies are Improving Visual Management, our CEO and Co-founder Dr. Greg Jacobson and Mark Graban, our Vice-President of Improvement & Innovation Services and founder of LeanBlog.org, walked viewers through the ins and outs of improvement boards and how improvement software is helping organizations take their boards to the next level.
Watch the full webinar here:
What are Improvement Boards?
Graban introduced the webinar by making sure listeners knew improvement boards are not corporate boards, they are boards hung up in workplaces to share improvement information. These improvement boards are what you might call an element of Lean management practices, what a lot of people would call or daily Lean management, Graban explained.
“When I first got involved in healthcare 10 years ago, there was no shortage of bulletin boards in hospital settings. But those boards usually just accumulate information over time with nothing ever being taken down. There’s clutter, you can’t find the most urgent information, so we don’t mean just typical bulletin boards,” said Mark, continuing to explain that barren boards are also not good improvement boards.
“The key is to make sure the board is being populated. It’s not the board that’s important, but the engagement and the leadership behaviors. If you have the board without a methodology or the right leadership that board is just going to end up being a different kind of waste of space than the super-cluttery announcement board.”
Having a problem they aim to solve will keep these boards from becoming corporate wallpaper as the phrase would suggest, Graban said.
There are several problems an improvement board can resolve, including:
- Lack of information (information deficit)
- Lack of alignment
- Lack of communication
- Lack of collaboration
- Lack of improvement (which may be caused by any of the other deficiencies)
“If people are putting up boards and not using them, then I think we should ask why. Is the board in some way not proving helpful to people? Boards, I think at a high level, visualize information for people, whether they are physical boards or virtual boards,” Graban explained.
Types of Improvement Boards that Work
Graban listed several types of improvement boards organizations using continuous improvement methodologies utilize to visualize their improvement efforts, including:
Huddle Boards / Status Boards
Huddle boards share recent results, updates, and local information that a team will find helpful. This information should be very tactical and short-term focused. It should include things that a team can huddle around and talk about on a daily basis.
Metrics Boards
Metrics boards look at local performance measures and, hopefully, attempt to connect local results to strategy deployment or higher-level goals and alignment. These boards often include charts and have color coding to help visualize that performance.
SQDC / FMDS Boards
Safety Quality Delivery Cost (SQDC) boards and Floor Management Development System (FMDS) boards, which is an expression used by Toyota, are board systems commonly found in manufacturing.
“The purpose of the board is not just to drive results, but it’s also about developing managers, developing staff - which is a very Toyota way of looking at things - developing people, and getting results,” Graban explained.
Kaizen Boards/Idea Boards
Kaizen or idea boards help illustrate problems, opportunities for improvement (OFI’s), and ideas, as well as provide status/updates and evaluation of different ideas and problems.
Boards Sharing Completed Kaizens
Boards that share completed Kaizens motivate staff by displaying what was done, what was fixed, who was involved, and what the impact was.
Strategy Deployment Boards
Strategy deployment boards, which you might find in executive boardrooms, visualize important level goals and measures, but also look at activity and results, linking improvement activity to different goals that we’re trying to accomplish.
What Really Makes Improvement Boards Effective
No matter what type of board an organization chooses as most relevant to their improvement activities, one particular trait is incredibly important to the board’s success — visibility.
“My conclusion and as I’ve started seeing over the years, boards like this work great if you can see them,” Graban said.
“Now that we start reaching some of the frontiers of what you can accomplish with physical boards, it starts begging the question, how do we share improvements beyond the population of people who can physically stand in front of this board? How do we share improvements across departments and across sites within an organization? There are certain problems that start coming up, even though physical boards like this are solving one type of workplace problem, as we start doing more improvement we might start discovering different problems that virtual boards can help solve.”
How Digital Boards Improve Improvement Boards
Interestingly enough, Jacobson began learning about Kaizen and continuous improvement after reading Kaizen: The Key to Japan’s Competitive Success by Masaaki Imai, which doesn’t place a large emphasis on boards.
“So, I didn’t really understand the importance of boards, nor did boards really show up in the early versions of KaiNexus. And so a lot of what I’m going to talk about is not what we’ve come up with at KaiNexus, but what we’ve learned in working with our customers,” Jacobson said.
Jacobson outlined five ways technology can, and has, been helping organizations take their boards to a higher level. These include:
Collaboration
Jacobson, an ER doctor himself who regularly works overnight shifts, explained that the KaiNexus team speaks with people daily who are struggling with teams that are spread out into different areas in the United States and internationally, or that work different shifts.
“With a digital board, all of a sudden, the time and the space conundrum starts, maybe not perfectly getting broken down, but you start to break through barriers of space and time,” Jacobson said. “I still think problem-solving face-to-face is the gold standard, so when we’re thinking through digital boards we’re not thinking of this as a way to not do all of the things you would do with a physical board, we’re thinking about ways to augment that experience and bringing people into the conversation that couldn’t have been part of the conversation.”
Standard
Standard board options don’t necessarily produce identical boards, but they do mean help making decisions about board visuals, which may be what many organizations need to get started, Jacobson explained. Even better, in digital boards items can be changed and modified over time, further reducing barriers to getting started. Gone are the days when a design had to be finalized and minimums ordered from the printer, stocking organizations with hundreds of physical boards that couldn’t then be modified as their improvement efforts matured. Features in KaiNexus also allow personalization, so that managers can brand boards either for organization or for departments and work areas.
“So standardization does not mean that it has to be boring and not look pretty,” Jacobson said.
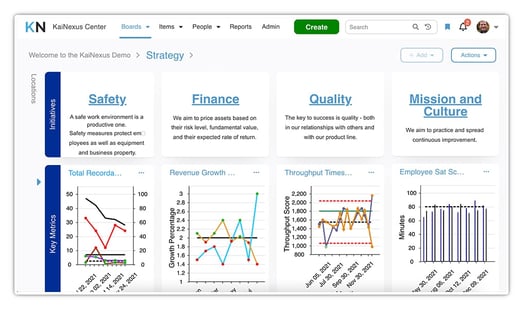
Visibility
“I would venture to say that 95 percent of the people listening to this webinar right now are continuous improvement experts; we live and breathe continuous improvement but what we’re trying to do is to get a whole bunch of non-continuous-improvement-experts to understand what we’re doing. And if they can’t see the improvement work, they’re going to have a really hard time participating in it,” Jacobson said.
Of course, with a digital system instead of being able to see one board in a location, you can literally see every single board across your organization.
Impact
“That’s one of the reasons why people come to us initially to start conversations -- they just have no visibility into the impact of their improvement work. Or to be able to aggregate and report on an impact becomes such an administrative burden that it doesn’t’ get done in anything real time and/or without a huge amount of effort,” Jacobson said.
When you’re doing the work in a continuous improvement platform, the software used to perform the work automatically generates reports for an organization's boards, eliminating any question about the impact of improvement efforts.
Knowledge Repository
In addition to automatically creating impact reports, the work that you do in continuous improvement also creates a knowledge repository for you with no additional effort.
“When you’re doing your work in a platform that’s optimized for you, all of a sudden you get things like searching capabilities and you can go back in time and see if people have worked on this. You also get things like making sure you’re not duplicating effort,” Jacobson said.
Additional Paper Board Problems Digital Boards Solve
While creating the webinar, Jacobson thought of a few other problems created by paper boards that digital boards solve for organizations, including:
Tracking Versus Doing
KaiNexus often hears from potential clients who are looking for a system to track improvements, or who are having difficulty tracking the status of improvements.
“A lot of times people are doing the work in email or in Gemba, and they’re so used to putting this in Excel that Excel actually becomes the complete tracking mechanism, and in many ways, there’s really not a lot of value in the process of sticking it into Excel,” Jacobson said.
“When you take that jump and you actually start doing the improvement work with active notifications, with creating your workflows, with putting in real-time updates, then you start getting into a situation where all of the reporting and all of the boards are almost a side effect, if you will, that are a benefit of simply doing the work in KaiNexus.”
Jacobson challenged webinar listeners not to think of it as needing something to track the work, but rather as needing a better productivity tool to do the work, where the side effect is tracking the work.
Waste
“One of the areas [of waste] is the updating of manual boards. So there’s this process of going into a system, filling something out, printing it out, walking to the printer, sticking it on the board, keeping it up that way,” Jacobson said. “And if that improvement is interdepartmental, and you’re trying to do cross-departmental collaboration, then you literally have to go update that on [multiple] different boards versus when your boards are digital, when that work actually gets done in the system those boards are automatically updated.”
Jacobson also challenged listeners to think about how many times an employee would simply not go to the idea board because of the amount of effort required or because it’s just is not practical.
How Do You Scale Yourself?
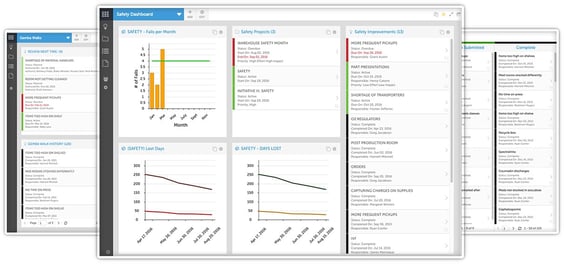
“We’re talking to continuous improvement experts all day long, and let me tell you, we don’t hear this sentence a lot: ‘Oh, man our continuous improvement department is so well staffed, we have such good ratios, we’re not overworked at all, we’re exactly everywhere where we need to be,’” Jacobson quipped.
“We talked to people that constantly say that they’ve literally 90 boards that they review on a quarterly basis. They have to go to two boards a day, four days a week, just to visit the board, just to see what the update on the board is, let alone if they actually need their help or to do any coaching.”
Of course, with software like KaiNexus, continuous improvement staff can check in on 90 boards in one day, finally allowing them to scale themselves.
Physical Space
“When you go digital, those kinds of physical space constraints go away and people are constrained by actual leadership behavior, by their own mental capacities, by their own improvement, and not by any kind of physical areas,” Jacobson said.
How to Make Digital Improvement Boards Work for You
After running through so many of the reasons why organizations would be better served by using digital boards instead of paper boards or Excel sheets, Jacobson discussed how organizations can create boards within KaiNexus. Showing how simple it is to add and maneuver lists, charts, reports, etc. on a digital board in KaiNexus Jacobson showed several examples.
KaiNexus customers now are often taking down the paper bulletin boards and replacing them with plasma screens, monitors, or projectors. The amount of inexpensive technology available to bring on-screen boards to frontline employees are plentiful and constantly increasing, making updating and engaging staff in real time the future of improvement boards.
If you would like to know more about how you can use KaiNexus to create digital improvement boards, you can book a custom demo here.
Watch the full webinar here:
Add a Comment