The DMAIC improvement cycle is a structured, data-centric approach to problem-solving. DMAIC (pronounced də-MAY-ick) stands for "Define, Measure, Analyze, Improve, and Control." It is an essential element of the Lean and Six Sigma business methodologies, but it can also be valuable for any organization looking to support continuous improvement.
Each phase of the cycle has a defined set of tasks and objectives. Let's have a closer look at each of them.
Define
During the first phase, Define, opportunities for improvement collected from process operators are selected for evaluation. This phase is required to create a picture of success and an understanding of the impact of the problem on all stakeholders.
The essential steps during Define are:
- Define and confirm the opportunity for improvement
- Mark the scope of the project
- Document customer requirements
- Define the business opportunity
- Estimate the impact of improvement
- Identify all stakeholders
- Select the team that will implement this improvement
- Draft the team charter
- Create a current state map for related processes
Success depends on the Define phase, so fight the temptation to hurry through this step and start experimenting with change. Thoughtful planning is the bedrock of structured improvement.
Measure
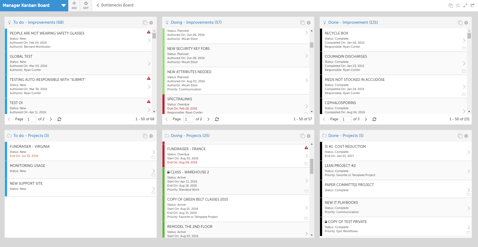
The Measure phase comes next. During this part of the cycle, the process to be improved is documented, and baseline metrics are established.
Important tasks include:
- Define the methods by which data will be collected to evaluate the impact of change
- Identify input, processes, and output performance indicators
- Collect and analyze current state data
Visual management tools can be helpful when working in the Measurement phase. Look to control charts to map process behavior and recognize deviation. Kanban boards are useful for visualizing process flow, and X-matrix can be valuable alignment tools.
Analyze
During the Analyze phase, your team will identify and test the root causes of problems to ensure that changes focus on the underlying reasons, not just the symptoms.
Tasks include:
- Agree on a problem statement
- Undertake a root cause analysis
- Implement process control measures
- Undergo regression analysis
- Develop measurable improvement experiments
- Draft a plan for improvement
Value stream mapping and the 5 Whys problem-solving technique are beneficial during the Analyze stage. After the opportunities for improvement are identified and documented, the plan for change will emerge.
Improve
Once you have comprehensive data and analysis, it's time to decide what changes should be implemented to improve.
At this point, most teams will:
- Discuss proposed solution ideas
- Define expected results and benefits
- Draft revised process maps and plans
- Identify a pilot solution and plan
- Share the project with all stakeholders
Improvement software plays a crucial role at this stage. Team leaders assign tasks and track activities as the project moves along. Alerts via email and in the application help keep progress moving and ensure that no tasks are skipped. Dedicated software makes cross-functional collaboration seamless by giving everyone a standard platform for data collection and task management. Organizational leaders and managers can keep tabs the progress of all DMAIC projects with configurable dashboards and charts.
Control
Once the changes are implemented, and data shows that the improvement was a success, it's time to ensure that the positive results will be lasting and that measurement will be maintained over the long-run.
Typical activities at this stage include:
- Verify reduction in defects or delays due to the targeted cause
- Consider whether additional improvements are needed to achieve the project goal
- Draft, document, and share the new Standard work
- Document and share the lessons learned
With improvement technology in place, you can schedule measurement activities over time to ensure that key performance metrics continue to show the expected results. You'll be able to quantify and share the total impact of the change in terms of efficiency, quality, cost, or customer satisfaction.
The Control phase lasts until someone identifies a new opportunity for improvement, and the cycle begins again.
Using the approach DMAIC requires discipline, but once your team gets comfortable, it will become second nature, allowing for more positive change quickly and efficiently.
Add a Comment