In 1986, Masaaki Imai introduced the world to the philosophy and practice of Kaizen in his book Kaizen, The Key to Japan’s Competitive Success. We highly recommend reading it if you are exploring ways to make your organization more efficient and better at achieving continuous improvement. (We’ll recommend a few other titles at the end of this post as well.) Our aim today is to share information about the framework of Kaizen. Hopefully, it will leave you ready to discuss the approach and eager to learn more.
What is Kaizen?
This is how Masaaki Imai him self described it, “Kaizen is everyday improvement, everybody improvement, everywhere improvement.”
The word kaizen is a mash-up of the Japanese words for “Good” (zen) and “Change: (kai). In the context of the workplace, Kaizen refers to practices and actions that continually improve all functions and include every employee from the C-suite to the front line. The kaizen approach was first developed by several Japanese automotive manufacturing businesses following the second world war. Since then, it has been embraced by organizations in every sector and everywhere across the globe.
The Principles of Kaizen
Kaizen is not an improvement process or a description of how to improve. Instead, it is a way of thinking that informs every decision and infuses the culture. Several structured improvement methodologies, including the Toyota Production System, Lean, and Six Sigma, are built on the philosophy of Kaizen. Several core beliefs are common to all organizations that practice Kaizen:
- Every process can be improved
- Continuous improvement is necessary to be competitive
- Defects and errors are almost always due to flawed processes, not people
- Each person in the organization must be involved in improvement work
- Incremental changes can have momentous impact
The Benefits of Kaizen
While Kaizen is often associated with Lean manufacturing’s emphasis on waste reduction, that is far from the only application of Kaizen. Practicing Kaizen can help you improve safety, productivity, quality, and customer satisfaction. There are also some less direct benefits that organizations enjoy:
- Employees are more engaged because they have a direct impact on the processes they operated.
- Employees are more emotionally committed because they have a sense of ownership.
- Employee retention improves.
- The organization is more competitive because of improved efficiency, lower costs, fewer defects, and more innovative products.
- Improved consumer satisfaction.
- Better problem-solving.
- More cross-functional collaboration.
How to Start a Culture of Kaizen
Engaged leadership is essential to any organization’s ability to proliferate the kaizen paradigm. Leaders must commit to providing the training and resources necessary to get the most out of the approach and enjoy sustained results. Some of the things leaders can do to help Kaizen thrive in an organization are:
- Lead by example. Get personally involved in improvement work and be visible and enthusiastic about it.
- Talk about Kaizen and what it means for the organization at every possible opportunity.
- Ask team members for ideas for improvement and make sure that there is a quick response when ideas are submitted.
- Empower employees to implement opportunities for improvement without fear of negative consequences if the results aren’t perfect.
- Broadcast successes far and wide.
- Concentrate efforts on small, incremental improvements.
- Ensure that employee incentives and goals are aligned with the overall purpose and objectives of the organization.
Technology and Kaizen
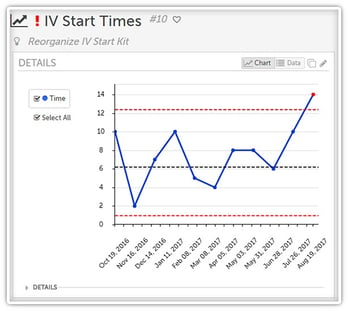
Of course, it is not strictly necessary to implement software to support the kaizen way, but it helps a lot.
If you invest in a software platform to collect opportunities for improvement, manage project, capture and report results, and broadcast success, you’ll put your organization in an excellent position to get the most value out of your kaizen culture.
The best solutions include features that support popular improvement techniques like control charts, digital huddle boards, X-matrices, and more. When you join the kaizen mindset with technology to support it, the results can be amazing.
Suggested Reading
As promised, here are a few outstanding resources in addition to Kaizen, The Key to Japan’s Competitive Success.
- Gemba Kaizen: A Commonsense Approach to a Continuous Improvement Strategy, Second Edition (2012) by Masaaki Imai - A second breakthrough book by Imai reveals how to implement cost-effective, incremental improvements that impact your most essential business processes.
- Creating a Kaizen Culture: Align the Organization, Achieve Breakthrough Results, and Sustain the Gains (2013) by Jon Miller, Mike Wroblewski, and Jaime Villafuerte - This book is all about employees, the most critical asset of an effective organization. You’ll get insight on how to increase engagement by creating a culture that embraces Kaizen, including examples from Toyota, Zappos, and others.
- Toyota Kata (2009) by Mike Rother - Learn how Toyota manages continuous improvement along with respect for people by making Kaizen an integral part of the culture.
We hope this post has you pondering ways you can put Kaizen to work in your organization to boost productivity, reduce waste, and delight customers and employees. We’ve seen it work for our customers and are sure it could have an impact on your organization and team.
Add a Comment