Summary
Waste exists in every business, often hidden within daily operations. The 8 wastes of Lean—defects, transportation, waiting, motion, overproduction, over-processing, inventory, and human potential—reduce efficiency and increase costs across all industries. Once you understand what to look for, you can systematically eliminate these wastes and significantly improve your operational performance.
Why Should Every Business Care About Lean Waste Elimination?
Waste elimination directly impacts your bottom line. While it might sound like an environmental initiative, Lean waste reduction is fundamentally about protecting profitability and improving operational efficiency.
These same 8 wastes appear consistently across industries—from software development to healthcare to construction. Every business has processes that deliver value to customers, and within those processes, waste naturally accumulates. The key is developing systems to identify and eliminate it systematically.
Industries successfully implementing Lean waste reduction include:
- Manufacturing and production
- Healthcare and medical services
- Software development and technology
- Construction and engineering
- Education and training
- Professional services
What Are the 8 Types of Lean Waste?
1. What Constitutes Defects and Mistakes Waste?
Defect waste is related to the time and materials spent doing something of poor quality and later fixing it or trashing it. Lean practitioners also count the inspection cost as part of this waste (although you shouldn't reduce inspection unless you've created perfect quality through mistake-proofing techniques).
Common examples across industries:
- Healthcare: Incorrect medication administration or dosing errors
- Manufacturing: Parts that fail quality control inspections
- Software: Bugs requiring debugging and patches
- Administration: Data entry errors requiring correction
- Logistics: Deliveries containing wrong or missing items
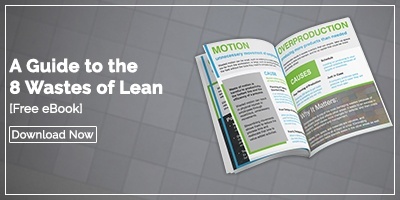
2. How Does Transportation Waste Impact Your Operations?
The waste of transportation involves moving inventory, people, tools, or other items more often or further than is necessary. Excessive movement can lead to product damage, unnecessary work, and exhaustion.
Key examples include:
- Healthcare: Unnecessary patient transfers between departments
- Retail: Returning overstock inventory to warehouses
- Manufacturing: Moving components between multiple work areas
- Logistics: Inefficient routing and delivery paths
3. When Does Waiting Become a Costly Waste?
Waiting involves customers, patients, or inventory sitting idle. Waiting happens when the person or item is ready for the next step, but the process is not prepared to accommodate them.
Common waiting scenarios:
- Healthcare: Patients in waiting areas
- Software: Code awaiting quality assurance review
- Business operations: Pending approvals from other departments
- Manufacturing: Production delays due to component shortages
- Service industries: Resources waiting for assignment
4. What Is Motion Waste and How Do You Spot It?
The waste of motion involves the unnecessary movement of people or items within a work center. It is often the result of neglecting the 5s'.
Examples include:
- General operations: Time spent searching for tools, materials, or information
- Office environments: Poorly organized workspaces requiring excessive movement
- Meetings: Gatherings that don't contribute to value creation
- Digital systems: Complex interfaces requiring multiple steps for simple tasks
5. How Does Overproduction Create Multiple Waste Problems?
Producing more of a product than can be consumed at the time creates the waste of overproduction. Making too much of something (or making it too early) creates other types of waste. Overproduction is of particular concern because it exacerbates transportation, inventory, and motion wastes.
Overproduction examples:
- Manufacturing: Producing components before downstream processes are ready
- Administrative: Creating unnecessary documentation or reports
- Food service: Preparing meals that exceed actual demand
- Retail: Inventory that exceeds sales capacity
- Content creation: Developing features or content with limited usage
6. What Qualifies as Over-Processing Waste?
Over-processing means doing work that does not add value to the customer. Over-processing is resolved with simplification. Sometimes, in Lean, the best approach is to stop doing some things instead of figuring out how to do them better.
Common over-processing activities:
- Data management: Entering identical information in multiple systems
- Approvals: Multiple authorization levels for minor expenditures
- Healthcare: Ordering tests that won't influence treatment decisions
- Reporting: Including data that stakeholders don't use
- Product development: Features that customers don't value
7. Why Is Excess Inventory Considered Waste?
The waste of inventory involves storing products or materials that are not needed. Excess inventory results in a waste of space, and it wastes the cost associated with the physical inventory. Although it is a significant concern in manufacturing, it occurs in other sectors as well.
Inventory waste examples:
- Marketing: Outdated promotional materials and printed forms
- Office operations: Overstocked supply storage
- Food service: Perishables that expire before use
- Equipment: Rarely used tools and machinery
- Information: Backlogged data entry and processing tasks
8. How Does Wasting Human Potential Damage Organizations?
For a long time, the discussion centered around only the prior seven Lean wastes, but more recently, the waste of human potential has joined their ranks, and with good reason. It is probably the most common and most damaging type of waste that organizations encounter.
Signs of human potential waste:
- Task misalignment: Employees performing work that doesn't leverage their capabilities
- Limited development: Absence of career growth and skill building opportunities
- Underutilization: Highly skilled workers performing routine tasks
- Ignored input: Employee improvement suggestions that aren't implemented
How Can Software Help Eliminate Lean Waste?
Continuous improvement software can significantly affect organizations serious about finding and eliminating waste in all of its forms. Here's how it helps:
Feature | Function | Business Impact |
Opportunity Capture |
Streamlined waste reporting and documentation |
Centralized identification and prioritization |
Standardized Work Documentation |
Current best practice |
Reduced process variation and errors |
Cross-Functional Collaboration |
Unified improvement platform |
Improved communication and coordination |
Progress Tracking |
Automated alerts and status updates |
Enhanced accountability and follow-through |
Impact Measurement |
Tying activities to business impact |
Quantifiable return on investment |
Success Recognition |
Employee acknowledgment and feedback |
Increased engagement in improvement activities |
Why Do Spreadsheets Fail for Waste Management?
Many organizations attempt waste tracking using spreadsheets, but this approach has significant limitations that prevent sustained improvement.
Spreadsheet limitations:
- Passive tracking: Requires manual updates and checking
- Limited accountability: No automated reminders or escalations
- Siloed information: Each department maintains separate versions
- Poor visibility: Difficult to track progress across multiple initiatives
Software advantages:
- Active management: Automated notifications and status tracking
- Integrated accountability: Clear ownership and deadlines
- Centralized data: Single source of truth for all improvement activities
- Comprehensive reporting: Real-time visibility into results and ROI
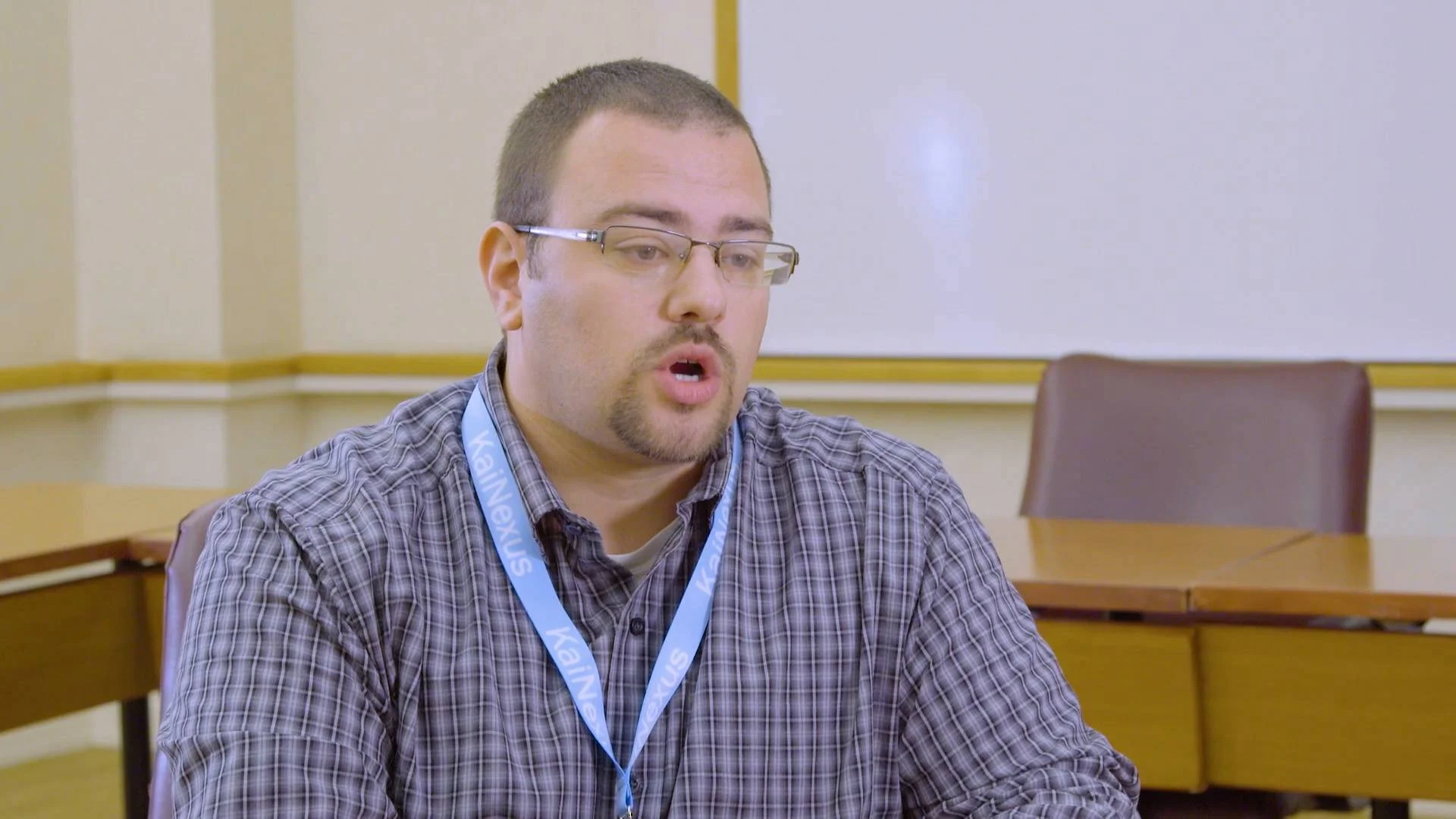
We want to challenge you to find specific examples of each of the eight wastes of Lean within your organization. Some may be glaringly obvious, while others are more subtle and harder to find. When you identify waste, you also uncover opportunities for improvement and move closer to becoming a more efficient and cost-effective organization.
Frequently Asked Questions About Lean Waste
What industries can benefit from Lean waste elimination?
All industries can benefit from Lean waste elimination. While originally developed for manufacturing, these 8 wastes consistently appear across healthcare, software development, construction, education, and service industries.
How do you prioritize which waste to eliminate first?
Focus on wastes with the highest impact on customer value and operational costs. Pay particular attention to wastes that create cascading effects, such as overproduction, which can amplify transportation, inventory, and motion wastes.
Can small businesses implement Lean waste reduction?
Small businesses often achieve faster results due to their operational agility. Start with basic observation and documentation of waste patterns before investing in comprehensive software solutions.
What role do employees play in waste identification?
Employees are essential for waste identification since they interact with operational processes daily. Establishing systems for employees to report improvement opportunities is critical for comprehensive waste elimination.
How do you measure the success of waste elimination efforts?
Key metrics include reduced operational costs, improved time to market, enhanced customer satisfaction, increased profitability, and employee engagement in improvement activities. Continuous improvement software simplifies tracking and reporting these measurements.
Add a Comment