Quality management is a subject that's often studied in business. There are hundreds of books and countless blog posts with advice on how to improve quality. Some organizations choose to adopt comprehensive process management methodologies like Six Sigma, Lean Manufacturing, or the Toyota Production System.
These systematic, structured approaches all have their place and can help the right situation, but you don’t have to fully adopt any of them to improve the quality of your results. There are some fundamental quality management things you can do to reduce waste and deliver more value to customers.
What is Quality?
Before we get into the techniques, we strongly recommend it is necessary to be clear about what quality means. People sometimes associate quality with the end product that is delivered to the customer.
If a company produces headsets, for example, a headset that meets customer approval is considered a quality win. But what if all headsets delivered to customers are perfect, but 5% required rework on the production line? Customers may be happy, but you still have a quality problem. What if the customer has a question about the headset, but he can’t get through to technical support? That’s another type of quality problem. What if the workers who made the headset didn’t get paid on time? You can be sure that they think there’s a quality problem.
The idea is that every process within an organization is subject to quality problems. When you look at how you manage quality in your organization, it’s essential to think very broadly about it.
Here are some things you can do immediately to start making process improvements.
Implement Standard Work
Standard work is the documented current best practices for performing each task or process. It’s a simple idea, but most organizations have multiple workers doing the same job in ways different enough to result in variation. Standard work eliminates that variation and ensures that every process is performed the same way every time. Once the task is standardized, improvements can be implemented in a structured way to move the process closer to a perfect result with no waste.
The process operators should always be involved in crafting the Standard work. Once complete, the documentation of the standard should be available in the workspace whenever it is needed. Standard work forms the basis of quality management and is a requirement for improvement.
The 5 Whys
When a problem arises, many organizations suffer from a tendency to blame people and jump to solutions. But when it comes to quality management, it turns out that almost all failures are failures of process. Yes, people make mistakes, but it’s rarely incompetence. It is often a problem related to training, lack of resources, poor workspace design, or an error-prone process configuration. To find the root cause of the problem, you can use the 5 Whys approach.
The 5 Whys technique is straightforward. When a process problem happens, team members ask “why” until the root cause is revealed. This usually takes about five repetitions. For example, a customer service team may have this conversation:
Our post-interaction customer satisfaction score decreased by 20% last week?
Why did our post-interaction satisfaction score decrease?
Our call abandon rate went up by 15%.
Why did our call abandon rate increase?
The average hold time went over 3 minutes.
Why did the hold time go over 3 minutes?
One of the customer service representatives was out sick, and there was no replacement resource available.
Why was there no replacement available?
The two backup team members were both on vacation.
Why were the two backup team members both on vacation at the same time?
The scheduling software did not flag that these employees should not be on vacation at the same time.
In this case, the low satisfaction scores were not the fault of the customer service representatives. The real problem was the configuration of the scheduling software. The team can choose to live with this risk or make technical changes to prevent it. The 5 Whys is powerful because it forces the team to challenge assumptions.
Control Charts
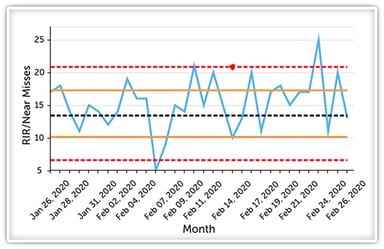
Control charts help supervisors and managers to differentiate between normal process variation and special cause variation that requires attention.
A process control chart is a simple graph used to visualize how a process performs over time. Data points are charted in time order with a central line for the average (or median), an upper line for the upper control limit, and a lower line for the lower control limit. By using process control charts, managers avoid overreacting to every up and downswing. They also address problems caused by only looking at average results instead of the variation. Here is a post that contains more detail about how they are used.
Each of these quality management techniques is useful for organizations of every size and level of complexity. Quality management software is the ideal way to help organize them daily and make them even more effective. If your team is committed to improving the quality of your process, these techniques are the perfect way to get started.
Add a Comment