When most people think about quality assurance (QA), they imagine the process of testing products before delivery to the customer. In software development, QA involves code inspection, user experience assessment, regression testing, test cases, and more. In manufacturing, it requires acceptance sampling, error proofing, statistical process control, and stress testing, among other things. The goal in both cases is to produce a product that will meet and exceed customer demands while minimizing variation and cost as much as possible.
Few companies release known material defects into the market, but many operate with known defects and messy workarounds for business processes. What if the quality assurance model for your product or service was also directed at every process in your business? Would the "customer" consider them each to be free of defects? Let's think about what it means to apply the quality assurance concept to the business as a whole.
What is the Role of Quality Assurance?
Producing Products for Customers
If you think about it, each business process produces a product or an outcome for a customer. Sometimes the customers are internal, and sometimes the "product" is invisible, but they're customers and products just the same. For example, entering a purchase order into the ERP system produces a payable invoice for the AP manager. Updating prospect records in the CRM makes a reliable forecast for the VP of Sales. When you look at every process through this lens and identify both the product and the customer, the opportunity for quality assurance systems to be applied emerges. There might be "defects" everywhere we look!
Finding Defects
Likely, both the people engaging in business processes and their internal or external customers can quickly identify defects in both the process and the results. We can define a defect as anything that doesn't go as it should in a process, even if the fault doesn't reach the end customer. These are the things that drive front-line employees crazy every day yet often escape the notice of top-level management. Applying the idea of product quality standards to processes elevates what may be seen as minor complaints to opportunities for improvement and defect reduction.
Culture of Quality
Thinking about the business in terms of quality assurance makes defect-free results everyone's top priority. Ignoring problems or implementing workarounds that only mask deeper issues becomes unacceptable as the culture embraces the quality mantra. Not only will this positively impact the targeted business processes, but ultimately, the goods and services provided to external customers will be delivered more profitably.
What are the Objectives of Quality Assurance?
When you ask everyone to become involved in implementing quality control within their functional area, it is helpful to outline a few of the critical objectives of a QA-centered organization.
Standardize Processes
Standard processes are essential to achieving and maintaining quality outcomes. Consistent results are unlikely if a function is operated differently depending on who does it or when it occurs. That doesn't mean that process can't change; they have to! But improvements should be thoughtful and result in a new standard definition.
Limit Variation
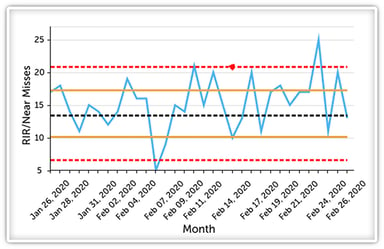
Some variation in process outcomes is normal, but process operators and managers seeking to ensure quality should look for variation that might represent a process problem or a worrisome trend. Control charts are an excellent tool for sorting out normal variation from data that is cause for concern.
Deliver Maximum Value to Customers
People don't always think of waste as a quality problem, but it is. Anything that doesn't add value to the customer introduces waste and opportunity for error into processes. Often, quality assurance is more about process simplification than product inspection.
The Benefits of Systemic Quality Assurance
Several remarkable things start to happen when every business process is subject to quality inspection. You can expect:
Improved Customer Satisfaction
Your customers ultimately decide whether your quality control has been effective. These days, customers don't keep their experiences to themselves. A bad interaction with your company can lead to negative online reviews, social media nightmares, and potentially even lawsuits. On the other hand, high-quality products and services can turn your customers into vocal advocates for your brand.
Increased Employee Engagement
Your employees want to be in the position to do their best work. When you empower them to introduce a quality assurance process, they develop an emotional investment in the outcomes of the procedures they operate. As a result, the amount of discretionary effort they are willing to expend increases.
Reduced Costs
The systematic introduction of quality assurance reduces costs in many ways:
- Built-in quality shrinks the need for and cost of the inspection.
- It decreases wasteful defects and reworks.
- It targets unnecessary activities and frees those resources for more productive ends.
- It eliminates minor workarounds that result in significant long-term added expense.
Better Forecasting
Quality assurance means having processes that are well under control. When you have standard work, measure results, and simplify operations, you can reliability predict things like how much raw materials will be needed, how long processes take, and how much each operation will cost.
Consistent Compliance
Many types of organizations are required to maintain compliance with regulations and laws. Still, others maintain voluntary compliance with certifications such as ISO or SOC 2 that give customers increased confidence. Achieving compliance is one thing, but keeping it up over time requires strict quality control beyond simple inspection.
Creative Innovation
When processes produce consistent results and high-quality outcomes are the norm, employees can start to think creatively about how to move each process closer to perfection. Defects and rework are stressful and can kill the drive to innovate. When the root cause of poor results is identified and corrected, the environment is more conducive to inspiration and ingenuity.
Universal Quality Assurance Techniques
The following quality assurance techniques can be applied to any operation in the organization.
PDSA
The PDSA (PLAN, DO, STUDY, ADJUST) improvement cycle can be applied to any business process. It is a structured method for assessing and resolving problems within a process. The team begins by identifying the problem. Next, they implement proposed fixes, study the results, and adjust if any additional improvement is possible. Following a PDSA cycle, the process standard is updated. When necessary, a new cycle is initiated.
The 5 Whys
The 5 whys is a simple yet powerful technique for identifying the root cause of a quality problem. Process operators and leaders ask "why" as many times as necessary to find the real reason for the defect or error. Each situation will vary, but usually, five times does the trick.
Gemba Walks
Gemba walks are a quality assurance technique borrowed from Lean manufacturing. During a Gemba walk, the leader or supervisor visits the workplace (Gemba means "real place" in Japanese) to show respect for workers, ask questions, and observe process operations. Following a Gemba walk, the leader reflects on what was observed and suggests opportunities for improvement.
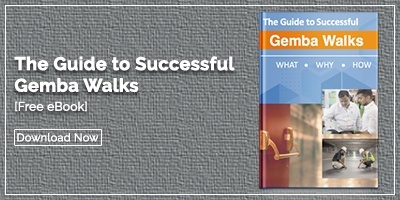
Rapid Improvement Events
In some cases, obvious quality problems justify a rapid improvement event in which stakeholders set aside other work for three to five days to focus on the issue at hand. The team starts with a charter identifying the problem and then works through the process of finding the root cause, examining and implementing potential solutions, and measuring results.
Sometimes positive change begins with a shift in mindset. A change to a holistic quality assurance mindset might be just what is needed to improve results for your organization. Something rarely offers so much benefit to shareholders, employees, and customers alike.
Add a Comment