One of the most critical concepts in Lean organizations is the idea that it is essential to eliminate waste. Why is it so central to the practice of Lean? The principles of Lean say that the ultimate goal is to provide perfect customer value. Anything that provides value to the customer is preserved. Everything else is considered waste. Some waste is inevitable due to physical constraints, regulations, or safety considerations. Still, most organizations find that they are engaged in many unnecessary activities and use more resources than is strictly required.
If you are striving to become a Lean organization, waste elimination is probably near the top of your list. Lean practitioners have identified particular types of waste, known collectively as the 8 Wastes of Lean. Certain types of waste are easy to spot and fix, while others are more difficult to detect.
Listen to the Episode:
1. Defects/Mistakes
Recently, I ordered a chair online. It's the sort that requires some assembly. When it arrived, the package was missing one of the legs. I contacted the seller, and they sent me a new one. They said the expense and hassle of returning the defective package were not worth the effort to keep it. There's not much I can do with a three-legged chair. This is a perfect example of how mistakes cause waste. Here are a few more:
- Software with bugs that has to be re-coded
- Misdiagnoses in healthcare that lead to unnecessary tests or treatment
- Products that are shipped to the wrong address
- Manufactured items that don't meet the customer's specifications
- Incorrect data entry
- Information that isn't communicated effectively or well understood
While it may be tempting to address the issue of defects with more inspection, the best resolution is to uncover the root cause, correct it, and error-proof the process.
2. Waiting
The waste of waiting takes two common forms. People and processes often must wait because the next step in the process isn't ready for them yet (waiting in line at a store, for example), or they are waiting because they don't have the inputs such as materials, work-in-progress, or information necessary to act.
- QA engineers waiting for code to be developed
- Emergency room patients waiting for test results
- Landscapers waiting for sod to be delivered
- Airplanes waiting for a gate to open up
- A completed entree waiting for garnish to be delivered to the pass
Kanban boards are a popular visualization tool for recognizing and responding to the waste of waiting.
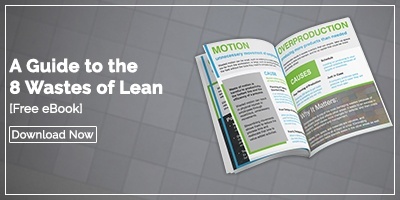
3. Transportation
Not all transportation is waste, of course, but the unnecessary movement of products, parts, equipment, or other items adds expense and risk to processes without adding value. Transportation applies to information as well. For example, using email to send files back and forth, rather than storing them in a central location, is electronic transportation waste. Other examples of the waste of transportation include:
- Sending unsold products from the store back to the warehouse
- Ordering parts or products from distant suppliers when closer options are available
- Moving equipment from one construction site to another
The waste of transportation is often related to poor workspace design. Other wastes like inventory and over-production contribute to the waste of transportation.
4. Motion
Motion is similar to transportation but involves unnecessary workspace activities. For example, one grocery store I visit is set up so the clerk removes an item from the basket and scans it. Another requires me first to move the item to the conveyor belt. I prefer the former, not because I'm lazy, but because it doesn't make sense to have two people handle and move each item when it can be done just as effectively by one.
Here are a few more examples:
- Software that requires ten clicks to get to the screen you want
- Workers searching for missing tools or office supplies
- Printers and other equipment that are not conveniently located
- Inadequately stocked examination rooms
Unorganized workspaces, processes without standardization, and inadequate understanding of customer behavior can all lead to the waste of motion.
5. Overproduction
Nowadays, just about everyone is familiar with just-in-time manufacturing and inventory management. Businesses are careful not to create products before there is demand, with good reason. Overproduction unnecessarily ties up resources and increases the likelihood of inventory and transportation waste. Overproduction can mean making too much of something or making it too early.
- Huge meals in restaurants
- Hospitals with more beds than the community needs
- Commuter trains with more cars than necessary
- Overstaffed retail stores
- Too many meetings or the wrong people in meetings
- Data that is entered separately into multiple systems
Overproduction is frequently caused by creating products based on forecasts rather than real-time customer demand.
6. Inventory
The wastes of inventory and overproduction go hand in hand. If a product is overproduced, it has to be stored somewhere, tying up space and requiring additional tracking and management. Depending on where the inventory is stored, it can also lead to wasted transportation and motion. Besides the obvious idea of unsold products sitting in a warehouse, the waste of inventory can be found in lots of places:
- Shelves of unused office supplies
- Too much bedside equipment in a hospital
- Stacks of promotional literature or pre-printed forms
- Perishable items that will go bad before they are used or sold
- Applications on your desktop that you never use
As with over-production, the best way to address inventory waste is to produce only what is requested by the customer.

7. Over-processing
When Lean practitioners talk about over-processing, we are talking about adding more complexity to a product, task, or process than is necessary to get the desired value. Over-processing is more than just a problem in manufacturing. It happens in every sector. Here's what it looks like:
- Software features that no one ever uses
- An MRI when an X-ray would suffice
- Identical data that is entered in more than one place on a form or software tool
- Complex purchasing processes with multiple approval levels
Frequently checking in to ask whether each element of the product or process is necessary is an excellent way to combat over-processing.
8. Human Potential
Perhaps the most damaging of all is the waste of human potential. Human potential is well-spent when employees use their whole breadth of skills, insights, and creativity. Organizations that fail to capture and act on employee ideas for improvement miss out on the fullness of what is possible. Wasted human potential can lead to employee turnover, increased absenteeism, and disengagement. It happens when:
- Time is spent correcting errors or responding to emergencies
- Employees do not have the opportunity to learn new skills or utilize hidden ones
- Employees are not involved in process improvement
- Workers are not given a chance to advance within the company
- Only a select few employees are engaged in positive change.
Maximizing human potential often requires a change of culture. Leaders who make the most of it involve as many people in decision-making, continuous learning, and process improvement as possible. They recognize that each person brings a new perspective and know that developing employee talent is the most efficient path to outperforming the competition.
The good news about waste is that every time you identify waste within your organization, you have found an opportunity for improvement. Reducing any of the eight wastes of Lean can significantly impact business results.
Add a Comment