Lean manufacturing is a process improvement methodology that started in the Japanese automotive manufacturing sector after World War II. Lean thinking aims to improve quality, speed production, and reduce costs by eliminating waste with continuous improvement driven by employees. Although the ideas were initially deployed in factories, the fundamental concepts apply to businesses of every sort. Today, Lean methods are used in hospitals, universities, construction, software development, and many other organizations.
A similar, data-driven approach to business is Six Sigma. It improves efficiencies and quality assurance based on reducing defects through process control and measurement. When the two methods are used together, the approach is called Lean Six Sigma. In any case, the bottom line is that many organizations benefit from a structured approach to continuous improvement. Many techniques, tools, and technologies support the journey to achieving an organization's short and long-term strategic goals.
The 5 Principles of Lean Manufacturing
Lean Thinking, by James P. Womack and Daniel T. Jones, covers the five principles of Lean manufacturing. Although the book is primarily focused on Toyota's achievement in revolutionizing manufacturing, the principles of Lean manufacturing can benefit organizations of every type.
1. Value
The value a customer places upon products and services determines how much money they are willing to pay for them (or if they want to pay for it at all). Lean thinkers insist on understanding precisely what drives customer value, including understanding what problem they are trying to solve. Critical focus is placed on what the customer will pay for specific products, features, and service offerings. Once this is determined, the producer is responsible for determining how cost and waste can be eliminated so that the product can be delivered profitably at the price the customer is willing to pay.
2. Value Streams
A value stream includes all the production processes, steps, and materials necessary to place the product (or service) in the customer's hands. Lean organizations seek to document and understand every aspect of their value streams, often using value stream mapping software to support this effort. This analysis will usually reveal time delays, activities that create value, activities that don't create value but can't be eliminated due to current technical, regulatory, or production limitations, and activities that create no value, making them wastes that become opportunities for improvement.
3. Flow
The "stream" analogy is continued in the third principle of flow. Just as water flows freely downstream, the value chain should experience a smooth progression from start to finish. Anything that increases the lead time or interrupts the flow of value contributes to the Lean waste of waiting and decreases the value to the customer. Maintaining flow requires careful synchronization of each internal and external supply chain aspect.
4. Pull
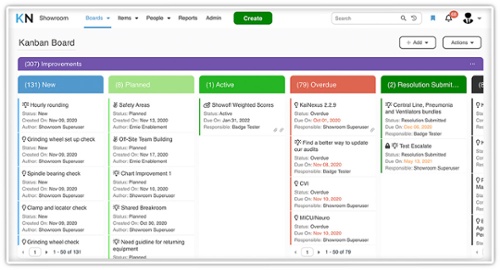
Rather than "pushing" production based on a forecast or schedule, those who use the pull system ideally don't make anything until the customer (internal or external) orders it. Visualization tools like Kanban boards help provide a mechanism for informing each step in the chain what they need to produce to meet the customer's needs.
5. Perfection
The final Lean manufacturing process principle from Lean Thinking is the relentless pursuit of perfection. Lean thinkers implement systems and measurements that continuously seek opportunities to improve, speed, and reduce the cost of each step of the value stream. When problems that impact quality arise, lean thinkers don't apply Band-Aids; instead, they seek and address root causes.
The beauty of these Lean principles is that they can be applied to assemble automobiles, move a patient from the waiting room to discharge, or develop a new software feature. Creating customer value while eliminating waste is the "secret sauce" of profitability no matter what you ultimately sell.
The 8 Wastes of Lean
Every organization seeks to eliminate waste, but those who practice Lean manufacturing take a systemic and structured approach. Lean leaders believe that every employee is in a position to recognize and reduce waste. To ensure this happens, supervisors and process operators are taught to understand eight distinct types of waste.
Inventory: The cumulation of raw materials or finished products that are not in demand by the internal or external customer is the waste of inventory. Excess inventory leads to unnecessary storage costs, potential spoilage, and wasteful administrative overhead.
Transportation: The waste of transportation is the unnecessary movement of products, equipment, or materials. Some transportation adds value, but any that doesn't is a target for elimination.
Motion: The waste of motion is similar to that of transportation. It involves the unnecessary movement of people. Motion is wasted when items aren't stored where needed, or equipment is inconveniently located.
Over Production: Over-production or the creation of products before the customer needs them leads to the waste of inventory and violates the principle of pull. Therefore, it is a common target of improvement in Lean organizations.
Over-Processing: Over-processing happens when features, packaging, services, data processing, or other operations don't add value to the customer.
Defects: Defects are perhaps the most obvious form of waste. They include products that must be reworked or discarded and the effort that goes into inspection and quality control. Rather than reduce defects through inspection, Lean organizations seek to find and fix the root cause of the problem.
Waiting: When the principle of flow is violated, the result is often the waste of waiting. One process can not proceed because it is waiting for input from another. When the concepts of pull and flow are well executed, waiting is eliminated.
Human Potential: While the waste of human potential was not listed initially among the wastes of Lean, modern leaders understand that employees are an enormous asset that should not be squandered. Therefore, in a Lean environment, employee ideas are valued, professional development is encouraged, and respect for people is foremost.
Lean Manufacturing Tools and Techniques
To achieve the goals of delivering value while reducing waste, Lean teams leverage various structured improvement techniques. Some of the most popular include:
Digital Huddle Boards: In the early days, organizations used physical boards to display improvement work in progress and often held daily stand-up meetings for updates and discussion. Today, improvement management technology offers digital boards that make it possible for everyone to stay on top of improvement efforts from any location at any time.
Strategy Deployment: Sometimes called Hoshin Kanri, strategy deployment is a technique for aligning improvement efforts to the organization's most important goals and objectives. When accomplished effectively, every employee understands how their work contributes to reaching the organization's true north.
X-Matrics: An X-matrix is a visualization tool used for strategy deployment. The organization's breakthrough goals, annual objectives, improvement opportunities, and metrics are defined along with the people responsible for each element.
Fishbone Diagram: Fishbone diagrams are a powerful visualization tool for problem-solving and analysis. They are designed to help users look at various categories of potential causes for problems so that the actual root cause can be identified and solved.
Kanban: Kanban is a method for supporting the principles of pull and flow. Work in progress is visualized so that managers and operators can spot any bottlenecks or gaps.
This post is not an exhaustive description of Lean manufacturing, but hopefully, it has covered some of the basics enough that your interest has grown. If so, our Lean Leadership Reading List is an excellent resource.
Add a Comment