Six Sigma and Lean manufacturing are business methodologies focused on improving the quality of goods or services an organization produces by reducing variance in the production process. Leaders know that when a production process lacks the stability to create high-quality output consistently, it will continue producing defective products until someone intervenes and improves the process. Reducing variation requires constant monitoring and measurement as systems tend to erode if not kept in check.
Over the years, Six Sigma and Lean practitioners have developed a set of workplace organization techniques and tools that address control, problem-solving, and improvement to eliminate defects and waste. Here are a few of the most essential.
1. Standard Work
Standard work is the documentation of the best practices for any process or task at that given moment. It is created and updated by the people who do the work. It forms the baseline for improvement and ensures process consistency.
Standard work includes information about how the workplace is organized, including where equipment and materials are stored and secured.
2. 5S Workplace Organization
An organized and well-stocked workplace is essential in the quest to eliminate variation. The popular 5S technique involves doing five things that all start with S in both English and Japanese.
The 5 S’s are:
Sort – Anything that isn’t required for performing operational tasks is removed from the area. Eliminating unnecessary clutter makes it easy for the items that are needed to be found quickly.
Set – Setting things in order involves ensuring that each item in the workplace has a specific place where it is stored and secured if needed. This approach minimizes the risk of something getting lost or misplaced and ensures that things aren’t damaged because they aren’t correctly stowed.
Shine – Keeping equipment, tools, materials, and the facility in good working order eliminates many potential problems. Tasks associated with shine include standard maintenance, cleaning, and repairing items that need attention.
Standardize – As we mentioned above, every workplace should have standards in place that everyone follows. Standardization involves defining ownership of various assets and tasks to help make the work environment predictable.
Sustain - Sustaining an organized workplace is the most challenging step of all. Keeping the workplace in order should not be an afterthought. There must be a plan to revisit each of the other four items and someone who owns the responsibility.
3. Control Charts
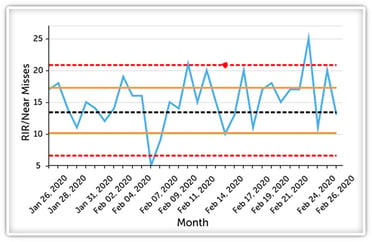
A process control chart is a graph used to track how a process behaves over time. Data points are plotted in time order in a chart with a central line for the average (sometimes a median), an upper line for the upper control limit, and a lower line for the lower control limit. Process control charts help leaders avoid panicking over every up and down swing. They circumvent problems caused by only looking at average results instead of the variations of results.
4. Gemba Walks
The Japanese word “Gemba” means the real place. During a Gemba walk, the manager goes to where work is done to show respect for the employees, ask questions, and potentially identify opportunities for improvement.
Gemba walks are an excellent way to ensure that the workplace standardization results of 5S are maintained. Managers or operators often take a checklist that includes the various 5S items on their walks. They can identify anything that is not 5S compliant and document it to be fixed or improved later. When performing a 5S review, it is helpful to closely look at every step of each process and task to ensure all improvement opportunities are identified. Doing so regularly will help facilitate continuous improvement and serve to sustain workplace organization gains as they are made.
5. Hoshin Kanri
Hoshin Kanri, also known as Policy Deployment, is a strategic planning approach designed to align the organization and ensure that everyone is working toward the same goals. The approach balances the need to achieve daily incremental improvement while moving toward the organization’s three to five-year breakthrough objectives at the same time.
6. Kanban
Kanban is a visualizing principle based on maximizing the flow of goods and work without unnecessary inventory or transportation. While initially used with physical cards at Toyota, Kanban has now moved to the cloud, and many organizations use digital Kanban boards to track the flow of work.
Kanban can also be used as a workplace organization technique by using signs, tape, and other marketings to indicate where items should be stored.
7. A3 Problem Solving
A3 is a structured problem-solving approach that gets its name from the size of paper that was used before digital tools became available. Thus, an A3 report is the result of an improvement cycle like DAMIC or PDSA.
A3 thinking is a management approach that turns day-to-day management into a learning practice for the whole organization. A3 management creates a standard method for innovation, planning, problem resolution, and sharing knowledge. The approach centers on organizational learning in the work itself. Therefore, it is sometimes referred to as operational learning.
8. Catchball
The Six Sigma technique of Catchball involves passing ideas from one person to another for feedback and action. The idea (ball) is set in motion when someone defines a challenge or opportunity. It then moves back and forth, up and down, or both until a plan is developed and agreed upon.
9. DMAIC
DMAIC is a five-phase improvement cycle;
10. PDSA
PDSA is an alternative improvement cycle that stands for Plan, Do, Study, Act. It is a simplified version of DMAIC that works best for improvement projects that are not heavy on statistics.
11. The 5 Whys
The 5 Whys is a brilliantly simple method of getting to the root cause of a problem or workplace organization failure. By asking and answering the question “why?” the basis of a problem can usually be found in five iterations.
12. Value Stream Mapping (VSM)
Value Stream Mapping is a tool for defining and assessing the movement of raw materials and work from the beginning of the process to delivery to the customer. It is how the current state of a function is documented and the basis for determining where waste can be eliminated or value-added.
This list doesn’t cover every workplace organization technique, but these are the necessities of the toolbox. You may find that you use all of them or only a few, but some combinations will likely help you achieve less variation as a rule and know how to respond when challenges arise.
Add a Comment